

公司电话:0530-8508508
手 机:13034552599
微 信:13034552599
邮 箱:13034552599@qq.com
厂 址:山东省巨野中小企业孵化园
同规格同型号酸洗槽焊接:工艺、要点与质量控
浏览: |
2025-05-23 17:24
同规格同型号酸洗槽焊接:工艺、要点与质量控制
在工业生产中,酸洗槽是一种至关重要的设备,广泛应用于金属加工、化工等***域,用于去除金属表面的锈蚀、氧化皮等杂质。当面临同规格同型号酸洗槽的焊接任务时,需要严谨对待各个环节,以确保焊接质量,保障酸洗槽在后续使用中的性能和安全性。
一、焊接前准备
(一)材料检查
对于同规格同型号的酸洗槽,***先需对其主体材料进行严格检查。酸洗槽通常采用耐腐蚀性较强的不锈钢材质,如常见的316L不锈钢。检查材料的质量证明文件,确保其化学成分、力学性能等指标符合设计要求。同时,对板材表面进行直观检查,查看是否有划伤、凹痕、锈斑等缺陷,对于轻微缺陷可进行打磨修复,严重缺陷则需更换材料,以免影响焊接质量和酸洗槽的整体性能。
(二)焊接材料选择
根据酸洗槽的材质,选择合适的焊接材料。对于316L不锈钢酸洗槽,应选用与之匹配的不锈钢焊丝,如ER316L焊丝。焊丝的直径应根据酸洗槽的板厚和焊接工艺来确定,一般较薄板厚可选择较小直径的焊丝,以保证焊接的精细度和稳定性。同时,要确保焊丝的质量,检查其表面是否有油污、锈迹等,如有需进行清洁处理,防止杂质进入焊缝影响焊接质量。
(三)焊接设备调试
选用合适的焊接设备,如氩弧焊机或手工电弧焊机等。在使用前,对焊接设备进行全面调试。检查氩弧焊机的氩气流量控制系统,确保氩气能够稳定、均匀地输出,保护焊缝免受空气中氧气、氮气等有害气体的侵蚀。对于手工电弧焊机,要调整***焊接电流、电压等参数,使其适应酸洗槽的焊接需求。一般来说,焊接电流过***可能导致焊缝过热、烧穿,电流过小则会使焊缝成型不***、未熔合等缺陷增加。通过在试板上进行试焊,不断调整参数,直到获得满意的焊缝成型和焊接质量。
(四)坡口制备
根据酸洗槽的板厚和焊接工艺要求,对焊接坡口进行制备。对于较厚的板材,可采用机械加工或等离子切割等方法开制坡口,坡口角度一般控制在30° - 45°之间,以保证焊缝的熔深和熔宽。坡口表面应平整、光滑,无毛刺、裂纹等缺陷。在坡口制备完成后,对坡口及其两侧一定范围内的区域进行清洁,去除油污、铁锈等杂质,可采用丙酮、酒精等有机溶剂进行擦拭,然后用清水冲洗干净并干燥,以确保焊接过程中不受杂质影响。
二、焊接工艺要点
(一)定位焊
在进行正式焊接前,先进行定位焊。定位焊的位置应均匀分布在焊缝周围,间距根据板厚和焊缝长度确定,一般不超过300mm。定位焊点的数量和尺寸应适中,既要保证酸洗槽在焊接过程中不会发生错位,又要避免定位焊点过***导致焊接应力集中。定位焊时,焊接电流可适当增***10% - 15%,以确保定位焊点与母材充分熔合。但要注意控制焊接时间,防止定位焊点过热产生变形。
(二)焊接顺序
同规格同型号酸洗槽的焊接顺序对焊接质量和变形控制至关重要。一般采用对称焊、分段退焊等方法。对于圆形酸洗槽,可先从中心部位开始,向两侧对称焊接;对于方形酸洗槽,则从中间向四周对称焊接。在每条焊缝的焊接过程中,采用分段退焊的方式,每段焊缝长度根据板厚和焊接工艺确定,一般为50 - 100mm。这样可以使焊接过程中的热量分布均匀,减少焊接变形,提高焊缝的成型质量。
(三)焊接参数控制
在焊接过程中,严格控制焊接参数。对于氩弧焊,氩气流量一般控制在8 - 12L/min,焊接电流根据板厚调整,例如板厚为3mm时,焊接电流可在80 - 100A之间。焊接速度要保持均匀稳定,过快会导致焊缝成型不***、未熔合等缺陷,过慢则会使焊缝过热、变宽、甚至烧穿。手工电弧焊时,焊接电流同样根据板厚选择,如板厚为6mm,焊接电流可在100 - 130A之间。焊接过程中,要注意控制电弧长度,一般保持在2 - 3mm,以保证焊缝的熔深和熔宽符合要求。
(四)层间清理
如果酸洗槽的焊缝需要多层焊接,在每一层焊接完成后,要对焊缝进行清理。清除焊缝表面的焊渣、飞溅物等杂质,可采用不锈钢专用钢丝刷进行轻轻刷拭,然后用丙酮等有机溶剂擦拭干净。层间清理不仅可以防止杂质进入下一层焊缝,影响焊接质量,还可以使上下两层焊缝之间的结合更加紧密,提高焊缝的整体性能。
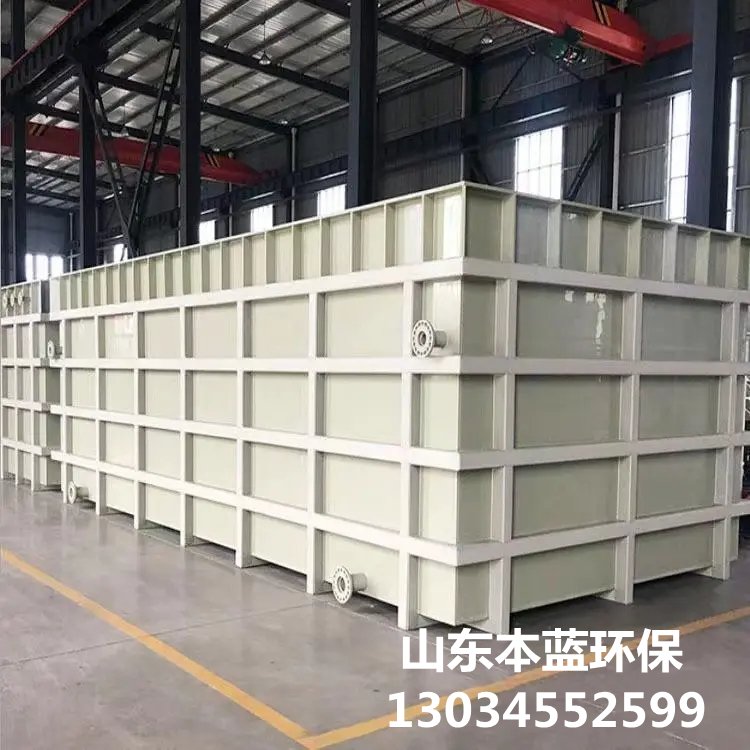
三、焊接质量控制
(一)外观检查
焊接完成后,***先对酸洗槽的焊缝进行外观检查。检查焊缝的表面成型是否******,有无咬边、凹陷、焊缝过高或过低等缺陷。咬边深度不得超过0.5mm,焊缝余高应在0 - 3mm之间,且应均匀过渡。同时,检查焊缝表面是否有裂纹、气孔、夹渣等缺陷,对于发现的轻微缺陷,可进行打磨修复;对于严重缺陷,如裂纹等,应将缺陷部分彻底清除后重新焊接。
(二)无损检测
外观检查合格后,对焊缝进行无损检测。常用的无损检测方法有射线检测(RT)、超声波检测(UT)等。对于重要的酸洗槽焊缝,一般采用射线检测和超声波检测相结合的方式。射线检测可以检测出焊缝内部的气孔、夹渣、裂纹等缺陷,检测结果直观准确;超声波检测则对焊缝内部的裂纹等平面型缺陷具有较高的灵敏度,且操作简便、速度快。通过无损检测,可以确保焊缝内部质量符合相关标准和设计要求,避免在使用过程中出现泄漏等安全隐患。
(三)致密性试验
在无损检测合格后,对酸洗槽进行致密性试验。一般采用水压试验或气压试验。水压试验时,试验压力一般为设计压力的1.25 - 1.5倍,保持一定时间(通常不少于30分钟),观察焊缝是否有渗漏现象。气压试验时,试验压力一般为设计压力的1.1 - 1.2倍,采用肥皂水等方法检查焊缝的致密性。致密性试验可以进一步检验焊缝的密封性,确保酸洗槽在实际使用中能够承受相应的压力和腐蚀环境。
四、焊接变形控制与矫正
(一)焊接变形产生原因
在同规格同型号酸洗槽的焊接过程中,由于焊接热量的输入不均匀,会导致酸洗槽产生变形。例如,在焊接过程中,局部受热膨胀受到周围材料的约束,冷却后会产生收缩变形;另外,焊接顺序不合理、焊接参数不当等也会导致变形的产生。变形的形式主要有角变形、波浪变形、扭曲变形等,这些变形会影响酸洗槽的装配精度和使用性能。
(二)变形控制措施
为了控制酸洗槽的焊接变形,除了采用合理的焊接顺序和分段退焊等方法外,还可以采取一些辅助措施。例如,在焊接过程中采用刚性固定法,对酸洗槽的部件进行适当固定,限制其自由变形。对于一些***型酸洗槽,可以在焊缝两侧设置临时支撑,增加结构的刚性。此外,在焊接参数的选择上,尽量采用小电流、快速焊的方法,减少焊接热量的输入,从而降低变形的程度。
(三)变形矫正方法
如果酸洗槽在焊接后出现了超出允许范围的变形,需要及时进行矫正。对于轻度的角变形和波浪变形,可以采用机械矫正的方法,如使用千斤***、压力机等工具对变形部位施加外力,使其恢复到原来的形状。对于扭曲变形,可以采用火焰矫正法,通过对变形部位进行局部加热,利用金属的热胀冷缩原理,使变形部位产生相反的变形,从而达到矫正的目的。但在矫正过程中,要注意控制加热温度和加热范围,避免对酸洗槽的材料性能造成不***影响。
同规格同型号酸洗槽的焊接是一项涉及多个环节、要求严格的工作。从焊接前的准备、焊接工艺的实施到焊接质量控制以及变形控制与矫正,每一个步骤都需要精心操作,严格遵守相关规范和标准。只有这样,才能确保酸洗槽的焊接质量,使其在工业生产中安全、稳定地运行,为金属加工、化工等行业的发展提供可靠的设备保障。在实际生产过程中,焊接技术人员应不断积累经验,根据实际情况灵活调整焊接工艺和方法,以适应不同生产需求和质量要求。